Using Fly Ash and Ground Blast Furnace Slag (GBFS) in concrete mixes as partial substitutes for Cement
- Many of the older concrete batching plants, often in lower turn-over areas have a single cement silo and some provisions for selected additives.
- Prolonging the life of the Plant will always be a major driver, but increasing its versatility is of almost equal importance.
- With the regular increases in the cost of GP and Special Purpose cement products, we think it make sense to look at ways to lower your production costs and at the same time, increase the quality of your concrete mixes and provide more production options.
- One of the ways to achieve a production cost reduction is to add a second silo to a single silo plant for additions of Fly Ash and/or GBFS
- For economy of installation, an excellent option here is to install a bolted panel silo, designed for containerised transport and to be a relatively straightforward installation
- Sourced and designed through a reliable Australian Company familiar with all relevant Australian Standards, these silos are not overly expensive to purchase.
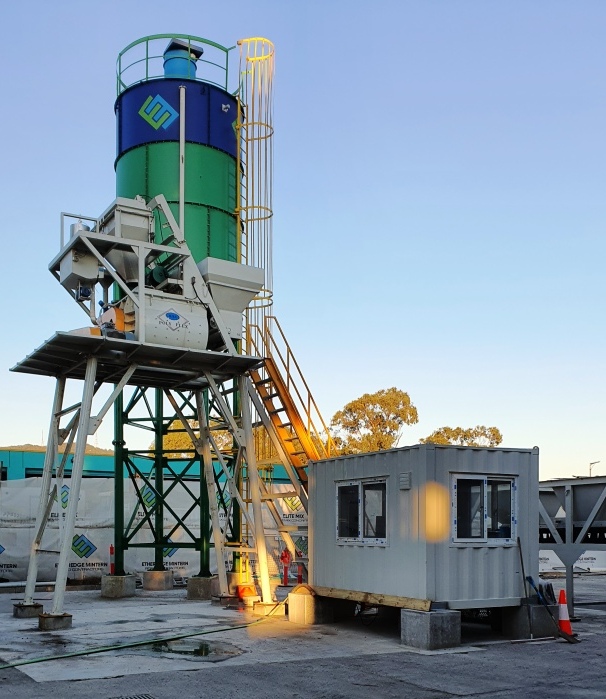
- One of the ways to achieve a production cost reduction is to add a second silo to a single silo plant for additions of Fly Ash and/or GBFS
- For economy of installation, an excellent option here is to install a bolted panel silo, designed for containerised transport and to be a relatively straightforward installation
- Sourced and designed through a reliable Australian Company familiar with all relevant Australian Standards, these silos are not overly expensive to purchase.
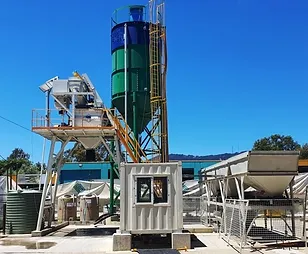